Photo by Marc PEZIN on Unsplash
THE REASONS FOR SEMICONDUCTOR SHORTAGE
In today’s market, the majority of the consumer and enterprise products are heavily equipped with semiconductor products (silicon chips). Over the last few years, the share of semiconductors in modern products has increased steadily. From automotive to smartphone to smart devices to aerospace, everywhere semiconductors are present. This has made semiconductors the building blocks of modern infrastructure.
These semiconductor products (silicon chips) require a lot of precision and time to manufacture. Any gaps in the manufacturing flow can eventually have negative consequences, which not only has an impact on the semiconductor manufacturers but also on the end products that are using these tiny silicon’s, and this is exactly what is happening since 2020.
Semiconductor Shortage Is A Combination Of Both The Design And The Manufacturing.
Shortage in the semiconductor industry not only impacts the semiconductor industry itself, but it ends up costing a lot to all the companies that are heavily reliant on these products. This is why automotive production has been halted, consumer electronics are not available easily in the market, and many other several consequences.
So, what is the reason for the semiconductor shortage?
Shortage in the semiconductor products is not because of one specific reason. To stop an industry like semiconductor from manufacturing, several negative factors have to come together. Unfortunately, this is what has lead to the shortage of semiconductors as the factors affecting it have introduced gaps in the manufacturing flow.
Below are the major contributing factors for the semiconductor shortage:
Forecast: Forecasting is an important part of ensuring that there is no wastage and all the customer demands are met in time. This eventually leads to efficient supply chain management. However, the forecast is not always accurate. It relies on many factors. This can range from market demand, a customer moving to a new solution, better cost alternative, and many more. For the semiconductor shortage that started in 2020, the reasons are majorly due to the market demand. Due to COVID-19, several facilities have to be closed down and this forced consumers and businesses to work remotely. This leads to the sudden surge in demand for smart solutions (one of the several such surges) and eventually increased the semiconductor demand (breaking the forecast). This prompted the companies to play safe by stocking (manufacturing) more devices than planned, which eventually put pressured on the semiconductor manufacturing capacity which lead to slow movement of silicon development, eventually putting them through the tough time of managing never seen before capacity management.
Shutdown: Semiconductor FABs are designed to run 24×7. The facilities are so complicated that any kind of shutdown can take weeks to recover, and will eventually lead to a shortage in silicon chip delivery which in turn halts the product of several other dependent industries (automotive for example). This exactly is what has happened in the last few months. Some FAB has to be shut down due to COVID-19, some due to extreme weather climate, and few due to fire hazards. All the FABs that were impacted were large facilities catering to the core products/solutions. Once a shutdown happens it becomes difficult to re-run the FAB quickly without proper checks to ensure there are no blocking points during the manufacturing flow.
Advanced Node: A smart product is made of different electronic chips. Each of these chips is using a different technology-node. However, the smartest and the most critical pieces in these devices are using the most sophisticated technology-node out in the market. Unfortunately, there are not many semiconductor FABs that are making advanced nodes. This puts a lot of dependency on these FABs and any shortfall in the production is eventually going to have an impact on the end product. The surge in demand in one segment (relying on the advanced node) has lead to a shortage of silicon products (using advanced node) in the other market segment. There is no time to expand the facility and this has eventually lead to the shortage of advanced node silicon.
Human Resource: Semiconductor FAB is highly automated but eventually does require human intervention. There are several tasks that have to be carried out manually and all these tasks are part of building the production wafers. COVID-19 lead to the curtailing (for their own safety) of people inside the FAB and this slowed down the production movement. The slowing of FABs is not good for the industry relying on semiconductor products. This eventually leads to slow production and contributed to the shortage.
Supply: Supply is not only about shipping the semiconductor product out of the FAB. It is also about ensuring the wafers and assembled part keep moving ahead till the end product has been assembled. Unless and until all the silicon chips are available, the end product (television for example) cannot be assembled. The semiconductor shortage is not about all the silicon products that go insider a device (for example smart camera), it is more about several other components that come from different FABs and facilities. Any supply constrains any of one the supply points can introduce shortage.
The above points are a handful amount of reasons. In reality, there can be more valid reasons for the shortage. In the long run, the semiconductor industry will overcome all the shortages and will also learn from them.
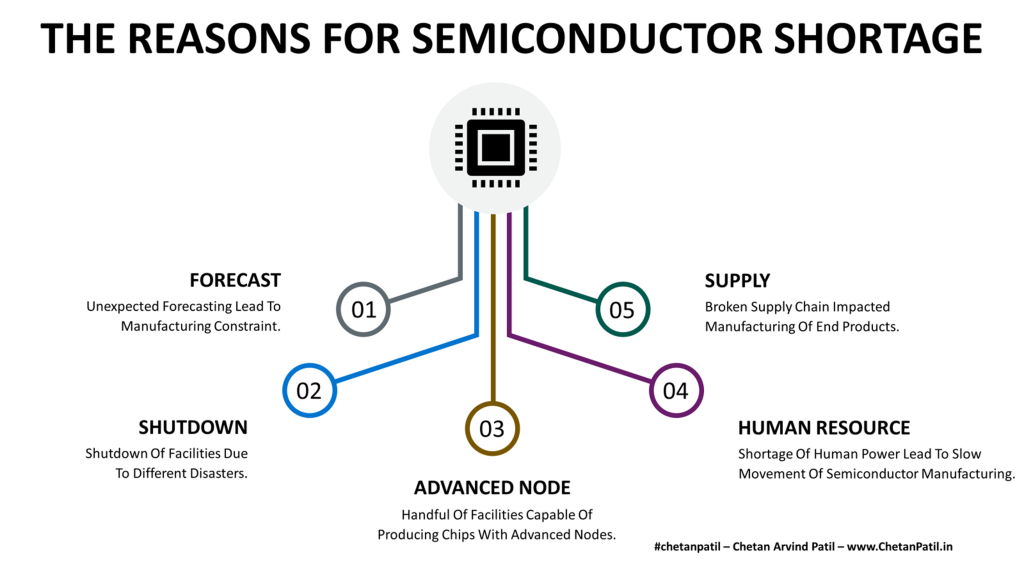
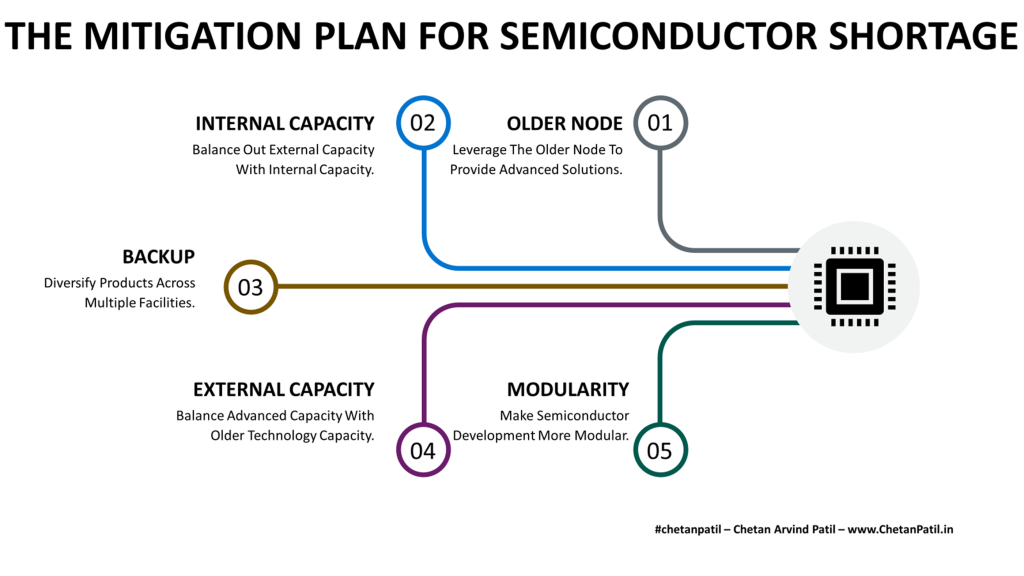
THE MITIGATION PLAN FOR SEMICONDUCTOR SHORTAGE
Shortage of any product (groceries to cars to semiconductor) eventually does get over. It indeed takes time and also leaves behind learnings that should be leveraged to overcome any such scenario in the near term.
When it comes to a high-tech industry like semiconductors, there is no single answer to semiconductor shortage avoidance. The shortage in the first place was contributed due to many factors. Based on the market situation below are the few points that can help mitigate the shortage in the future:
Older Node: Moving all the critical semiconductor solutions to the advanced node without building capacity is not the way forward. The FAB-LESS/IDM semiconductor design houses have to go back to the drawing board and understand how to diversify the technology-node usage based on the available capacity. Of course, the technology combination should eventually meet the specification, but the end goal should be to also consider how the market capacity (reality) is and will there be any capacity constraint if different shortage reasons come together again in the near future.
Internal Capacity: While IDMs already have the internal capacity that they can leverage to capture sudden increase in semiconductor demand. However, there needs to be a thorough review of what type (solutions) of capacity is in-house and how to balance the capacity against the external one. This can allow any of the external capacity shortages to be absorbed internally and thus helps in mitigating any pitfall.
Backup: Semiconductor products eventually get tied to a specific manufacturing flow that includes FABs and OSATs. It takes years to move these products to newer facilities. This is why semiconductor companies should start qualifying their products for multiple facilities to ensure any gaps/shortage at one location is fulfilled by the backup option.
External Capacity: Pure-Play foundries are very crucial to the semiconductor industry. They play an important part in ensuring that the product meets the end customers’ demand. However, in the last couple of decades, there has been growing reliance on external capacity. There is nothing wrong with it and not all semiconductor companies can put so much money in the semiconductor FAB. Still, the problem arises when there is a constraint in the external capacity as external can be pre-booked or pre-occupied by any entity in the world. This puts pressure on other semiconductor design houses that rely on external capacity but do not have enough capacity pre-booked. This has promoted an important discussion to build more external capacity that caters to not only today’s demand but to the demand of the next few decades.
Modularity: Both the design houses and the manufacturing facilities will have to quickly adapt to the modular approach. This modular approach can be about using any technology-node possible and also using any semiconductor manufacturing facility that is available. This will be a daunting task but should be doable.
Semiconductor design and manufacturing both play a crucial role in product development. Shortage in the semiconductor product is not only about the manufacturing but also about the design constraint that hinders flexibility in the manufacturing flow.
This is why the semiconductor shortage in 2020/2021 should not only be seen from the manufacturing aspect but also from the design point of view too.